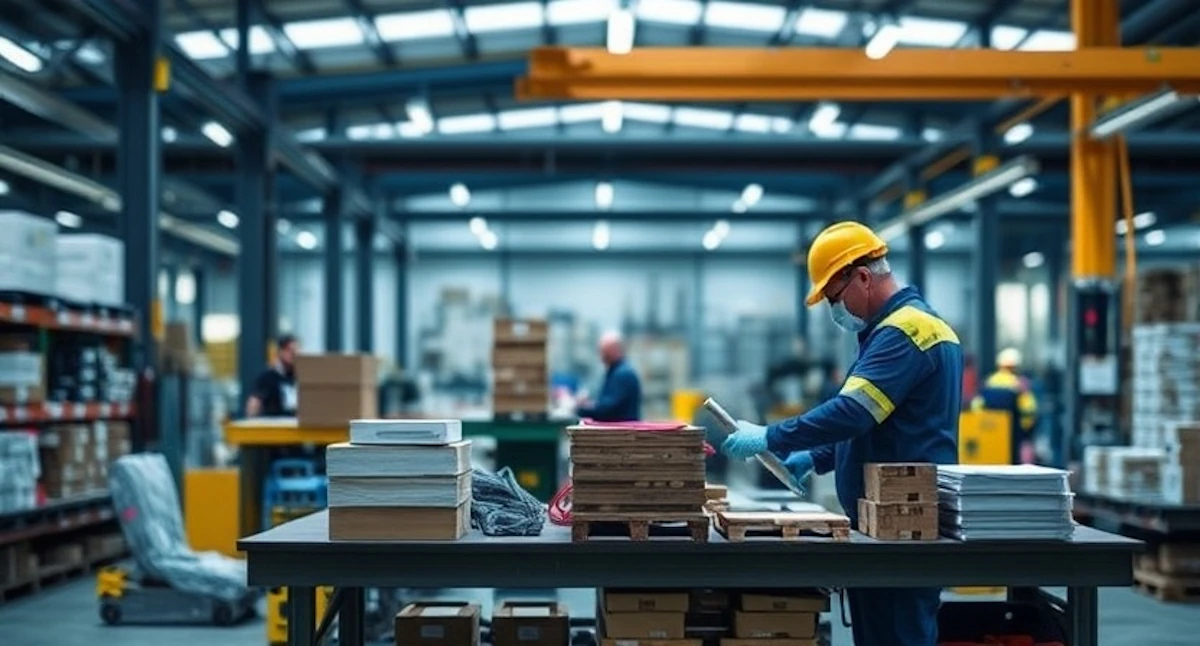
Quality control (QC) is a critical component in the procurement and management of industrial supplies. Ensuring that the products meet specified standards not only safeguards operations but also enhances customer satisfaction and compliance with regulatory requirements. This comprehensive guide will explore how to assess quality control in industrial supplies, focusing on best practices, methodologies, and key performance indicators (KPIs).
1. Understanding Quality Control in Industrial Supplies
1.1 What is Quality Control?
Quality control refers to the systematic process of ensuring that products and services meet specific quality standards and requirements. In the context of industrial supplies, this includes evaluating materials, components, and equipment to ensure they are suitable for intended use and meet industry standards.
1.2 The Importance of Quality Control
Quality control is essential for several reasons:
- Operational Efficiency: High-quality supplies contribute to smoother operations, reducing downtime and maintenance costs.
- Safety Compliance: Many industries are governed by strict safety regulations that necessitate adherence to quality standards.
- Cost Management: Poor quality can lead to increased costs associated with rework, returns, and customer dissatisfaction.
- Reputation Management: Consistently high-quality supplies can enhance a company’s reputation, leading to increased customer loyalty.
2. Key Components of Quality Control
To effectively assess quality control in industrial supplies, it’s important to understand its key components:
2.1 Specifications and Standards
Every industrial supply should come with clear specifications and standards that outline quality expectations. This may include:
- Material Specifications: Details on the composition, grade, and physical properties of materials.
- Performance Standards: Benchmarks for how the product should perform under specific conditions.
- Safety Standards: Compliance with regulations such as OSHA or ISO that dictate safety measures.
2.2 Inspection and Testing
Regular inspection and testing are vital for maintaining quality control. This can include:
- Incoming Inspection: Evaluating supplies upon receipt to ensure they meet specifications.
- In-Process Inspection: Monitoring production processes to catch defects early.
- Final Inspection: Conducting thorough checks before products are shipped to customers.
2.3 Documentation and Traceability
Maintaining thorough documentation is critical for quality control. This includes:
- Quality Control Records: Keeping detailed records of inspections, tests, and corrective actions.
- Traceability: Ensuring that products can be traced back through the supply chain, which is essential for recalls or quality issues.
3. Assessing Quality Control Processes
To assess quality control in industrial supplies effectively, consider the following methodologies:
3.1 Establishing Quality Control Guidelines
Create clear guidelines that outline the quality control process for each type of supply. This should include:
- Acceptance Criteria: Define what constitutes acceptable quality for each product or material.
- Testing Protocols: Specify testing methods and frequency.
- Roles and Responsibilities: Assign quality control tasks to appropriate personnel.
3.2 Supplier Evaluation
Assessing suppliers is a crucial step in quality control. This includes:
- Supplier Audits: Conducting regular audits of suppliers to evaluate their quality control processes.
- Certifications: Verifying that suppliers hold relevant quality certifications (e.g., ISO 9001, Six Sigma).
- Performance History: Reviewing historical data on supplier performance, including defect rates and delivery reliability.
3.3 Implementing Quality Control Tools
Utilizing quality control tools can enhance assessment capabilities. Some common tools include:
- Statistical Process Control (SPC): Utilizing statistical methods to monitor and control processes.
- Failure Mode and Effects Analysis (FMEA): Identifying potential failure points and assessing their impact.
- Root Cause Analysis (RCA): Investigating the underlying causes of quality issues to prevent recurrence.
4. Key Performance Indicators (KPIs) for Quality Control
Establishing KPIs is essential for measuring the effectiveness of quality control processes. Some important KPIs to consider include:
4.1 Defect Rate
The defect rate measures the percentage of defective products relative to the total number of products produced. A low defect rate indicates effective quality control.
4.2 First Pass Yield (FPY)
First Pass Yield assesses the percentage of products that meet quality standards without requiring rework. A higher FPY signifies better quality control.
4.3 Customer Complaints
Tracking customer complaints related to quality can provide valuable insights into potential issues. A rise in complaints may indicate underlying quality problems that need addressing.
4.4 Supplier Performance Metrics
Monitor supplier performance based on metrics such as on-time delivery, quality ratings, and compliance with specifications. This helps assess the reliability of suppliers.
5. Best Practices for Quality Control in Industrial Supplies
To ensure effective quality control, consider implementing these best practices:
5.1 Develop a Quality Control Plan
Create a comprehensive quality control plan that outlines processes, responsibilities, and timelines. This plan should be regularly reviewed and updated to reflect changes in operations or regulations.
5.2 Foster a Quality Culture
Promote a culture of quality within the organization. Encourage employees to prioritize quality and provide training on quality control practices and principles.
5.3 Utilize Technology
Invest in technology to enhance quality control processes. Consider using:
- Quality Management Systems (QMS): Software solutions that streamline quality control processes, document management, and reporting.
- Automated Inspection Tools: Technologies such as sensors and cameras can assist in real-time quality inspections.
5.4 Conduct Regular Training
Regular training sessions for employees involved in quality control are essential. Training should cover:
- Quality Control Techniques: Familiarize employees with inspection methods, testing protocols, and documentation practices.
- Regulatory Compliance: Ensure employees understand relevant regulations and industry standards.
6. Challenges in Quality Control Assessment
While assessing quality control is essential, several challenges can arise:
6.1 Inconsistent Standards
Inconsistent standards between suppliers can lead to complications in quality control assessments. Establishing clear, standardized specifications across the supply chain can mitigate this issue.
6.2 Resource Constraints
Limited resources, including time and personnel, can hinder effective quality control. Prioritize quality control activities and consider outsourcing some processes if necessary.
6.3 Data Management
Managing and analyzing quality control data can be overwhelming. Implementing a robust data management system can streamline this process and provide valuable insights.
7. Case Studies: Successful Quality Control Assessments
7.1 Case Study 1: Aerospace Manufacturer
An aerospace manufacturer implemented a rigorous quality control system that included regular supplier audits and performance evaluations. By establishing clear quality standards and utilizing SPC tools, they reduced their defect rate by 30% over two years, leading to increased customer satisfaction and lower operational costs.
7.2 Case Study 2: Automotive Supplier
An automotive supplier faced challenges with rising defect rates and customer complaints. By adopting FMEA and conducting root cause analysis, they identified critical failure points in their production process. Implementing corrective actions led to a 40% reduction in defects and improved relationships with key customers.
8. Future Trends in Quality Control for Industrial Supplies
8.1 Increased Automation
As technology advances, automation will play a larger role in quality control processes. Automated inspection tools and artificial intelligence (AI) will enhance the ability to monitor and control quality in real-time.
8.2 Data-Driven Decision Making
The use of big data analytics will allow organizations to make more informed decisions regarding quality control. Predictive analytics can help anticipate quality issues before they arise, enabling proactive measures.
8.3 Emphasis on Sustainability
As industries shift towards sustainable practices, quality control assessments will increasingly focus on environmental impact. Suppliers that demonstrate sustainable practices will likely gain a competitive advantage.
9. Conclusion
Assessing quality control in industrial supplies is essential for maintaining operational efficiency, ensuring safety, and enhancing customer satisfaction. By establishing robust quality control processes, utilizing effective tools, and measuring performance through KPIs, organizations can significantly improve their quality management practices.
As industries continue to evolve, staying abreast of quality control trends and challenges will be crucial for long-term success. By prioritizing quality control, businesses can not only meet regulatory requirements but also build a reputation for excellence in their respective markets.